With injection molding, the cycle time is very short (as low as 10 seconds). This allows for a high volume of parts to be produced in a small amount of time.
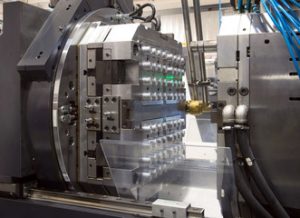
Design flexibility is another key benefit. This can include factors like weld lines, gate placements, corner transitions and rib designs. Read on Injection Mold Plastic Material Florida for more information.
ABS (acrylonitrile butadiene styrene) is one of the most common types of plastic used in injection molding. It is an impact resistant, strong, and durable material that’s widely used in a variety of consumer electronics and automotive parts. This plastic is easy to work with and can be molded into complex shapes, making it a popular choice for manufacturers looking for stylish and functional components.
Unlike thermosets, thermoplastics can be repeatedly heated without degradation. Once they reach their melting point, the polymer liquefies and can be easily injected into a mold. This allows for a more efficient production process, allowing manufacturers to produce products at a lower cost than would be possible with other materials.
When used for injection molding, ABS can be molded into complex shapes that provide both aesthetic and structural benefits. The dimensional stability offered by ABS makes it suitable for parts that need to maintain their shape over time, such as the housing of a power tool or the plastic protective covering on wall sockets. The durability and strength of ABS can also make it ideal for automotive components, such as dashboards and instrument panels.
While ABS is a versatile material that’s used in many different industries, it does have some limitations. It can be prone to warping and shrinking, which can affect the quality of the final product. It’s important to find a manufacturer that uses high-quality equipment and has extensive experience in manufacturing ABS injection molded parts. They should be able to provide real-time monitoring and control systems for their injection molding processes. This will help ensure that the resulting ABS parts are high-quality and meet their required dimensions accurately.
HDPE
HDPE is an injection mold plastic material known for its durability, strength, and chemical resistance. This commodity plastic is used in a wide range of consumer and industrial products. The injection molding process allows manufacturers to produce products with precise geometries, reducing production costs and improving quality.
Injection molding of HDPE is a dependable and economical method for producing long-lasting items. The melted plastic is injected into a mold, which is then cooled to solidify the plastic. This is a crucial step, as the proper cooling time prevents warping and distortion of the final product. After solidification, the molded part is ejected from the mold, which may require additional post-processing to ensure it meets aesthetic and functional requirements.
Injection-molded HDPE can be produced in a variety of shapes and sizes, making it suitable for many different applications. The material is also resistant to chemicals, moisture, and abrasions, which make it ideal for demanding environments. HDPE injection molded parts can be made with precise geometries and have excellent tensile strength, which reduces manufacturing costs and improves quality.
Injection molded HDPE can be used in a variety of applications, including the manufacture of thread protectors that safeguard pipe threads during transport and storage. The material is also commonly used in construction for items like pipe fittings and geomembranes, thanks to its corrosion resistance, durability, and longevity. It is also used in medical devices and equipment such as syringe plungers, IBM-made IV bags, and medical packaging, due to its bio-inertness and sterilizability.
LDPE
LDPE, or low density polyethylene, is a flexible plastic with a lower molecular weight than HDPE (high-density polyethylene). It can be molded under relatively high pressures without the problems that are often associated with injection molding of HDPE. This makes LDPE an excellent choice for injection molding of small, lightweight components and products with complex shapes. LDPE is also available in clear forms, which is helpful for many applications where visual clarity is important.
Injection mold plastic material is an essential part of the manufacturing process, but selecting the right one depends on a number of factors. Choosing a plastic that is the best fit for your product’s function, aesthetics, and durability will maximize its usefulness.
Among the most common plastics used in injection molding, LDPE is known for its versatility and affordability. Its unique flexibility and durability make it a good choice for applications that require high levels of chemical resistance, such as plastic containers for beverages and food. It can also resist bending and twisting, which is beneficial for packaging.
This type of plastic can be recycled, which is a great way to conserve resources and support environmental sustainability. In the recycling process, LDPE items are first melted and then reshaped into new plastic materials such as plastic bags and construction materials. These new products can be reshaped and reused for the same purpose as the original product, saving energy and resources.
LDPE is an excellent plastic for food packaging because of its non-toxic and odorless properties. In addition, it is resistant to moisture and chemicals. However, this material is not as durable as other plastics. It can be prone to scratching and may degrade under intense heat. Therefore, it is not recommended for use in outdoor applications.
PBT
PBT is a thermoplastic polyester resin that can be used to make plastic injection molding parts for a variety of industries. This material has excellent rigidity and thermal stability, and it resists chemicals well. It also has a low friction coefficient and can be combined with lubricants to improve wear resistance. PBT is easy to process and mold, making it a great choice for applications that require high precision and tight tolerances.
PBT can be used to manufacture a wide variety of products, from automotive parts and electronics to consumer goods and home construction. Its durability and high performance have earned it a place among the rising stars of engineering plastics. PBT is an excellent alternative to metals in automotive components and exterior panels, as it can withstand impact damage. It also offers good chemical resistance and can be sterilized without losing its physical properties.
Like most polymers, PBT can be molded by injection molding or extrusion. Its low melting point allows for rapid processing times and reduced energy consumption. It also has a relatively low moisture absorption rate, which helps ensure superior dimensional stability in finished products.
This plastic is available in a range of grades, including unreinforced and glass fiber reinforced varieties. It can also be reinforced with minerals, such as talc and mica, to enhance its strength and stiffness. Some grades of PBT are flame-retardant, offering additional safety benefits for a range of uses.
PBT is also an ideal option for cosmetic packaging, benefiting from its resistance to the chemicals typically found in these products. It is also highly rated for its mechanical performance, including electrical insulation and resistance to wear and tear.
Nylon 66
Nylon 66 is one of the most popular types of nylon used for injection molding. Its combination of strength, chemical resistance, and dimensional stability makes it ideal for a wide range of applications. It is also resistant to heat distortion and can withstand high temperatures, making it suitable for applications such as automotive under-the-hood components and electrical enclosures. Additionally, Nylon 66 has excellent impact resistance and tensile and flexural modulus. It is also available in a variety of colors and grades, allowing for greater design flexibility.
Nylon plastics are also highly flexible, which makes them ideal for complex geometries and demanding environments. However, it is important to keep in mind that the material can be prone to warping and shrinkage, which can negatively affect the finished product. To minimize these issues, it is crucial to optimize the injection molding process and mold design. This can be accomplished by adjusting the barrel temperature, screw speed, and injection pressure, as well as minimizing moisture absorption.
Injection molding is an essential part of the production process, and various quality control measures are used to ensure that final products meet strict standards. One such measure is visual inspection, where trained personnel inspect the molded parts for defects and deviations from specifications. Other quality control methods include testing for physical properties, such as density and tensile strength.
The price of Nylon 66 fluctuated in Q2, reflecting the broader market dynamics during this time. Supply of the feedstock caprolactam remained tight, while downstream industry offtakes slowed as a result of COVID-19 concerns. In addition, consumption taxes on imported mixed aromatics in China impacted demand.